DATASHEET
POWDERRANGE® 17-4
Applicable specifications: ASTM A564/A564M
Associated specifications: UNS S17400, AMS5643, ASME SA564, ASTM A705, DIN 1.4548 (X5CrNiCuNb17-4-4), DIN 1.4542 (X5CrNiCuNb16-4), AISI 630
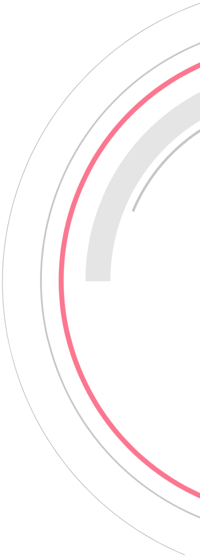
Type analysis
Single figures are nominal except where noted.
Iron | Balance |
Nickel | 3.00–5.00 % |
Niobium + Tantalum | 0.15–0.45 % |
Carbon | 0.070 % |
Chromium | 15.00–17.50 % |
Manganese | 1.00 % |
Nitrogen | 0.10 % |
Phosphorus | 0.040 % |
Copper | 3.00–5.00 % |
Silicon | 1.00 % |
Oxygen | 0.10 % |
Sulfur | 0.030 % |
Description
PowderRange® 17-4 stainless steel is a martensitic precipitation/age-hardening stainless steel offering high strength and hardness, along with excellent corrosion resistance, up to 600°F (316°C). It has good fabricating characteristics and can be age-hardened by a single-step, low-temperature treatment, which can be chosen to achieve specific strength and toughness combinations. Due to this balanced combination of performance and ease of use in AM, PowderRange® 17-4 for additive manufacturing has been used for a wide variety of applications, including rapid tooling functional components in nearly every market.
Key Properties
- Good strength, toughness, hardness, and ductility
- Good corrosion resistance
Markets
Applications:
- Surgical instruments and tools
- Valves and fittings
- Pumps and impellers
- Manifolds
- Industrial and chemical processing equipment
- Tooling
Powder properties
Part Number | PowderRange® 174 F |
Application | L-PBF1 |
Maximum Particle Size | Max 1 wt% > 53 µm2 |
Minimum Particle Size | Max 10 vol% < 15 µm3 |
LSD Percentile | D10, D50, D903, reported |
Atomization | Vacuum Induction Melted, Nitrogen Gas Atomized |
Apparent Density (G/CM3) | Measured according to ASTM B2124 and reported |
Hall Flow (S/50G) | Measured according to ASTM B2135 and reported |
1ASTM/ISO 52900: Laser—Powder Bed Fusion (L-PBF), Electron-Beam Powder Bed Fusion (EB-PBF), Directed Energy Deposition (DED)
2ASTM B214 Standard Test Method for Sieve Analysis for Metal Powders
3 ASTM B822 Standard Test Method for Particle Size Distribution of Metal Powders and Related Compounds by Light Scattering
4 ASTM B212 Standard Test Method for Apparent Density of Free-Flowing Metal Powders Using the Hall Flowmeter Funnel
5 ASTM B213 Standard Test Method for Flow Rate of Metal Powders Using the Hall Flowmeter Funnel
Testing of powder will fulfill certification requirements to Nadcap Materials Testing and ISO/IEC 17025 Chemical, per relevant ASTM procedures
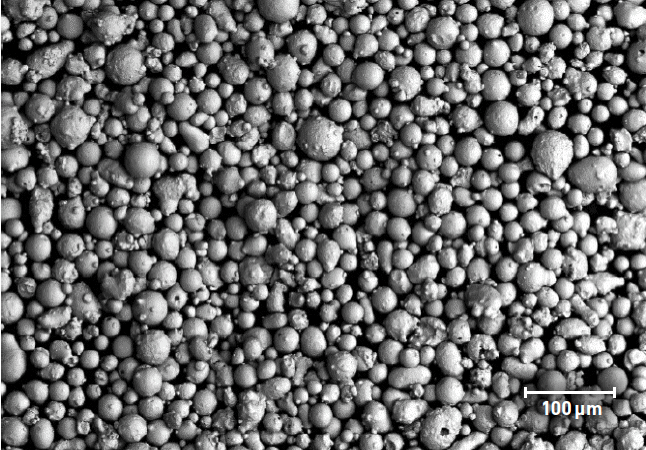
FIGURE 1—SEM IMAGE OF TYPICAL PowderRange 17-4PH POWDER
Additive manufacturing process guidance
ASTM/ISO 52900: LASER-POWDER BED FUSION (L-PBF)
Laser-Powder Bed Fusion(L-PBF) As-built
PowderRange 17-4PH is compatible with all commercially available L-PBF equipment.
To achieve mean, as-built density >99.9%, 20 to 60 μm layer thicknesses and Specific Energy ≥ 50 J/mm3 is recommended.
Stress relief
Homogenization (Hom)
Hot Isostatic Press (HIP/Sol/H900)
To achieve up to full density (100%): Process components under argon at not less than 14.5 ksi (100 MPa) at a temperature of approximately 2087°F (1141°C); hold at the selected temperature for approximately 240 min then cool under inert atmosphere to below 800°F (427°C).
Follow with Solution Anneal and Age treatment as described below
Solution Annealand Age Condition (Hom/Sol/H900)
After either homogenization or HIP’ing, Solution Anneal at 1900°F (1038°C) per ASTM A564/A564M for 0.5 hours, cool to below 90°F (32°C) to achieve complete transformation to martensite.
Sections under 3 in. (76 mm) can be quenched in a suitable liquid quenchant (e.g. water or oil) and sections over 3 in. (76 mm) should be rapidly air cooled. It is recommended not use this Solution Annealed condition, without age hardening, for the final product due to susceptibility to stress-corrosion cracking.
After Solution Anneal, age material as desired per ASTM A564/A564M, e.g. 900°F (482°C) for 1 hour and air cool, per ASTM A564/A564M.
Note: due to the higher nitrogen content of PowderRange 17-4PH, complete transformation to martensite may not occur during heat treatment, resulting in slightly lower mechanical properties as compared to PowderRange 17-4PH AR. If typical cast/ wrought PowderRange 17-4PH properties are desired, we recommend PowderRange 17-4PH AR as a superior alternative.
Machinability
PowderRange 17-4PH is readily machined in both the solution-treated and various age-hardened conditions. In the solution-treated condition, it machines similarly to stainless steel types 302 and 304.
When using carbide tools, surface speed feet/minute (SFPM) can be increased between 2 and 3 times over the highspeed suggestions. Feeds can be increased between 50 and 100%.
Corrosion resistance
IMPORTANT NOTE: The following 4-level rating scale (Excellent, Good, Moderate, Restricted) is intended for comparative purposes only and is derived from experiences with wrought product. Additive manufactured material may perform differently; corrosion testing is recommended. Factors that affect corrosion resistance include temperature, concentration, pH, impurities, aeration, velocity, crevices, deposits, metallurgical condition, stress, surface finish, and dissimilar metal contact.
Nitric Acid | Good |
Phosphoric Acid | Restricted |
Sea Water | Restricted |
Humidity | Excellent |
Sodium Hydroxide | Moderate |
Sulfuric Acid | Restricted |
Acetic Acid | Moderate |
Salt Spray (NaCl) | Good |
Sour Oil/Gas | Restricted |
For additional information, please
contact your nearest sales office:
The mechanical and physical properties of any additively-manufactured
material are strongly dependent on the processing conditions used to
produce the final part. Significantly differing properties can be obtained by
utilizing different equipment, different process parameters, different build
rates and different geometries. The properties listed are intended as a
guide only and should not be used as design data.
The information and data presented herein are typical or average values
and are not a guarantee of maximum or minimum values. Applications
specifically suggested for material described herein are made solely for the
purpose of illustration to enable the reader to make his/her own evaluation
and are not intended as warranties, either express or implied, of fitness for
these or other purposes. There is no representation that the recipient of
this literature will receive updated editions as they become available.
Unless otherwise specified, registered trademarks are property of
CRS Holdings Inc., a subsidiary of Carpenter Technology Corporation.
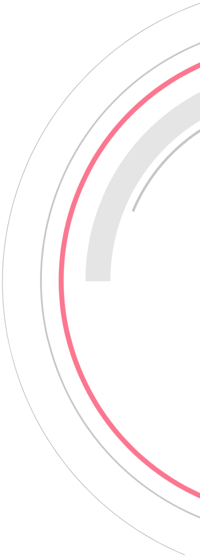