DATASHEET
POWDERRANGE® 316L
Applicable specifications: ASTM F3184
Associated specifications: AMS5648, ASME SA479, ASTM A276, ASTM A479, QQ-S-763, MIL-S-862, AMS5653, ASTM A182, ASTM A314, DIN 1.4404, ISO 5832-1, SAE J405 (316L), UNS S31600/S31603
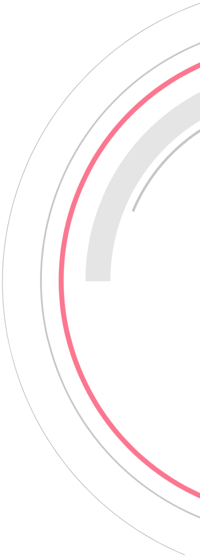
Type analysis
Single figures are nominal except where noted.
Iron | Balance |
Molybdenum | 2.00–3.00 % |
Nitrogen | 0.10 % |
Carbon | 0.030 % |
Chromium | 16.0–18.0 % |
Manganese | 2.00 % |
Oxygen | 0.10 % |
Sulfur | 0.030 % |
Nickel | 10.0–14.0 % |
Silicon | 1.00 % |
Phosphorus | 0.045 % |
Description
PowderRange® 316L is a low carbon, non-magnetic, austenitic stainless steel that exhibits moderate to good strength, good fracture toughness, and has generally good corrosion resistance, especially intergranular corrosion. It has excellent weldability in laser and electron-beam additive manufacturing processes and can be processed in either argon or nitrogen shielding gas.
PowderRange® 316L cannot be strengthened through post processing heat treatments but can be solution annealed to improve corrosion resistance. Solution annealing is application-specific, but is generally not necessary for most situations. Post processing can include traditional machining, abrasive flow machining, shot-peening, grinding, polishing, chemical milling/etching, and other methods.
Key Properties
- High impact toughness and good ductility
- Moderate strength and creep resistance
- Good corrosion resistance
Markets
Applications:
- Instrumentation devices
- Valves and fittings
- Pumps and impellers
- Manifolds
- Medical implants
- Tooling
Powder properties
Part Number | PowderRange® 316L F | PowderRange® 316L E |
Application | L-PBF1 | EB-PBF or DED1 |
Maximum Particle Size | Max 1 wt% > 53 µm2 | Max 10 wt% > 106 μm2 |
Minimum Particle Size | Max 10 vol% < 15 µm3 | Max 10 wt% < 45 μm2 |
LSD Percentile | D10, D50, D903, reported | |
Atomization | Nitrogen Gas Atomized | |
Apparent Density (G/CM3) | Measured according to ASTM B2124 and reported | |
Hall Flow (S/50G) | Measured according to ASTM B2135 and reported |
1ASTM/ISO 52900: Laser—Powder Bed Fusion (L-PBF), Electron-Beam Powder Bed Fusion (EB-PBF), Directed Energy Deposition (DED)
2ASTM B214 Standard Test Method for Sieve Analysis for Metal Powders
3 ASTM B822 Standard Test Method for Particle Size Distribution of Metal Powders and Related Compounds by Light Scattering
4 ASTM B212 Standard Test Method for Apparent Density of Free-Flowing Metal Powders Using the Hall Flowmeter Funnel
5 ASTM B213 Standard Test Method for Flow Rate of Metal Powders Using the Hall Flowmeter Funnel
Testing of powder will fulfill certification requirements to Nadcap Materials Testing and ISO/IEC 17025 Chemical, per relevant ASTM procedures
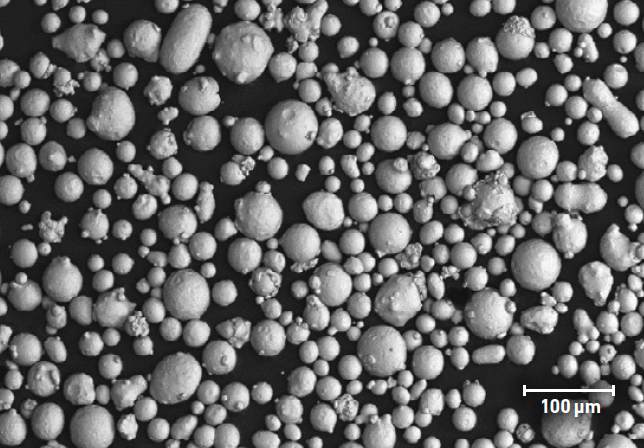
FIGURE 1—SEM IMAGE OF TYPICAL PowderRange 316L POWDER
Additive manufacturing process guidance
ASTM F3184: ADDITIVE MANUFACTURING STAINLESS STEEL ALLOY (UNS 31603) WITH POWDER BED FUSION
Laser-Powder Bed Fusion(L-PBF) As-built
PowderRange 316L for additive manufacturing is compatible with all commercially available L-PBF equipment.
To achieve mean, as-built density >99.9%, 20 to 60 μm layer thicknesses and Specific Energy ≥ 56 J/mm3 is recommended.
Stress relief
Stress relief may be performed per AMS2759, i.e. 700°F (371°C) for 1 hour, or substitute Solution Anneal per below for improved corrosion resistance.
Solution Anneal (Sol)
In many applications, PowderRange 316L may be used in the as-built condition or following a standard stress relief treatment on the build plate to reduce residual stress.
For greater corrosion resistance, a Solution Anneal treatment can be applied: 1900°F (1038°C) for 1 hour for every three inches of thickness, followed by a water quench.
Schedules better tailored to the AM process thermal history may be available. Please contact Carpenter Technology for information.
Hot Isostatic Press (HIP/Sol)
We recommend HIP as standard practice for microstructure homogenization; removal of residual spatter-induced voids, trapped gas porosity in powder and keyhole porosities; as well as to heal any shrinkage-induced micro-cracks in the material.
To achieve up to full density (100%): Process components per ASTM F3184 section 13: minimum pressure of 14.5 ksi (100 MPa) at a temperature of approximately 2087°F (1141°C) for 240 minutes in argon.
Follow with Solution Anneal treatment as described above to reduce sensitization and improve corrosion response.
Machinability
Stainless Type 316L machines with chip characteristics that are tough and stringy. The use of chip curlers and breakers is advised. To minimize work hardening, a strong positive heavy feed should be maintained; thus, the machines should have a minimum of backlash and the tool and workpiece must be rigidly supported. If possible, avoid very small cuts and feeds.
TYPICAL MICROSTRUCTURES
CONDITION
TRANSVERSE (X-Y PLANE)
LONGITUDINAL (Y-Z PLANE)
NOTES
As-built

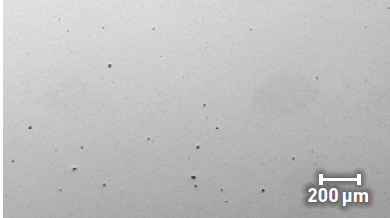
Mean densities greater than 99.9%
HIP/Sol
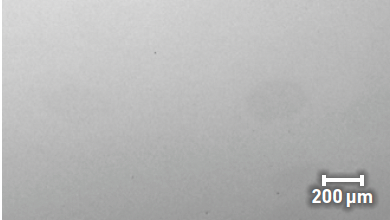
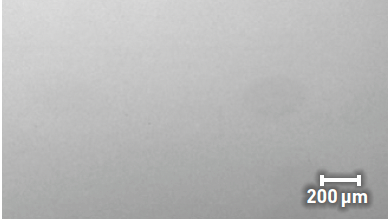
Up to 100% density
As-built, etched6
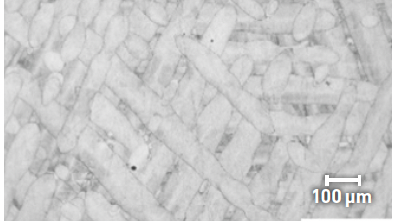
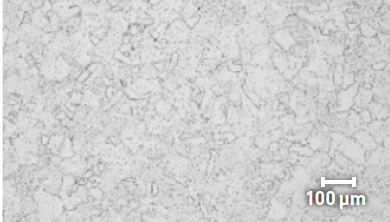
Clean weld tracks visible
Minimal spatter porosity
Sol, etched6
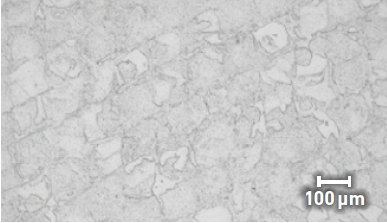
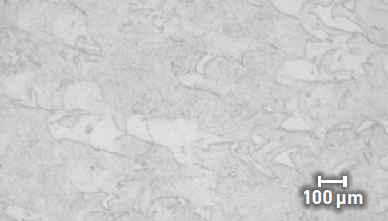
Minimal grain growth Weld tracks may still be visible Grain size ASTM 4-57
HIP/Sol, etched6
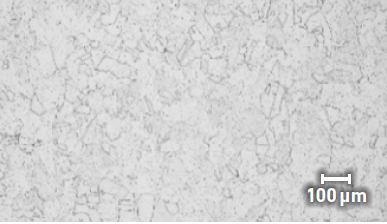
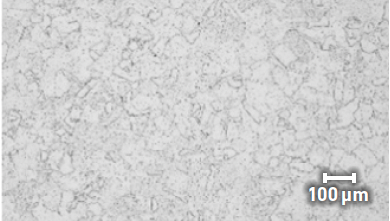
Homogenized microstructure Grain size ASTM 4-57
6 Etched with Ralph’s etchant
7 ASTM E112-13 Standard Test Method for Determining Average Grain Size
Typical achievable mechanical properties
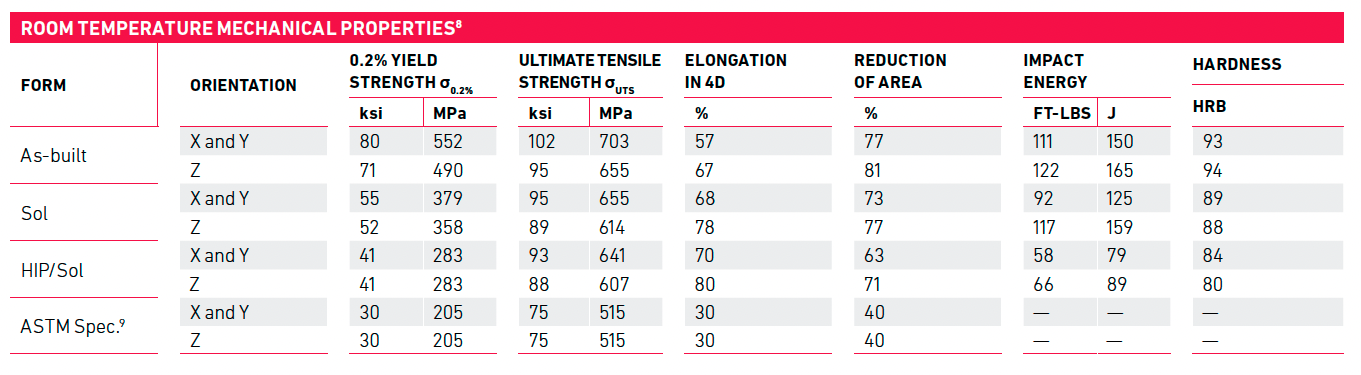
8Average of a minimum of 5 samples taken from across the extents of a build plate in each orientation and for each heat treatment. Testing performed in accordance with ASTM E8/E8M-16a (tensile), ASTM E23-18 (impact energy) and ASTM E18-19 (hardness). Additional data may be available through a wide range of consortia and other collaborations. Please contact Carpenter Additive for additional information.
9 ASTM F3184-16 Condition “A — Stress Relieved” Minimum Tensile Requirements
Corrosion resistance
IMPORTANT NOTE: The following 4-level rating scale (Excellent, Good, Moderate, Restricted) is intended for comparative purposes only and is derived from experiences with wrought product. Additive manufactured material may perform differently; corrosion testing is recommended. Factors that affect corrosion resistance include temperature, concentration, pH, impurities, aeration, velocity, crevices, deposits, metallurgical condition, stress, surface finish, and dissimilar metal contact.
Nitric Acid | Good |
Phosphoric Acid | Moderate |
Sea Water | Moderate |
Humidity | Excellent |
Sodium Hydroxide | Moderate |
Sulfuric Acid | Moderate |
Acetic Acid | Good |
Salt Spray (NaCl) | Good |
Sour Oil/Gas | Moderate |
Similar materials
Company |
Other Generic Names |
3D Systems |
GE (Concept Laser) |
EOS |
DMG Mori (Realizer) |
Renishaw |
SLM Solutions |
Alternative Title |
1.4404, 316L |
LaserForm 316L |
316L |
316L |
– |
SS 316L-0407 |
1.4404 (316L) |
For additional information, please
contact your nearest sales office:
The mechanical and physical properties of any additively-manufactured
material are strongly dependent on the processing conditions used to
produce the final part. Significantly differing properties can be obtained by
utilizing different equipment, different process parameters, different build
rates and different geometries. The properties listed are intended as a
guide only and should not be used as design data.
The information and data presented herein are typical or average values
and are not a guarantee of maximum or minimum values. Applications
specifically suggested for material described herein are made solely for the
purpose of illustration to enable the reader to make his/her own evaluation
and are not intended as warranties, either express or implied, of fitness for
these or other purposes. There is no representation that the recipient of
this literature will receive updated editions as they become available.
Unless otherwise specified, registered trademarks are property of
CRS Holdings Inc., a subsidiary of Carpenter Technology Corporation.
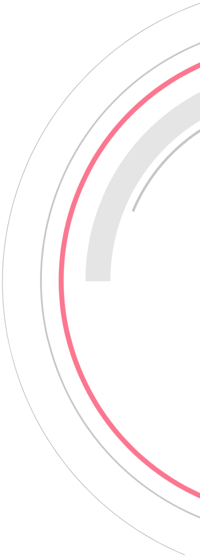