DATASHEET
SCALMALLOY®
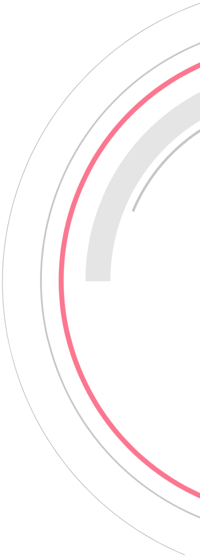
Type analysis
Single figures are nominal except where noted.
Aluminum | Balance |
Manganese | 0.30 to 0.80 % |
Silicon | 0.40 % |
Copper | 0.10 % |
Magnesium | 4.20 to 5.10 % |
Zirconium | 0.20 to 0.50 % |
Zinc | 0.25 % |
Vanadium | 0.10 % |
Scandium | 0.60 to 0.88 % |
Iron | 0.40 % |
Titanium | 0.15 % |
Oxygen | 0.05 % |
Forms manufactured
Powder |
Description
Scalmalloy is a powder product designed to be processed using laser-powder bed fusion (L-BPF) additive manufacturing. Due to high cooling rates and rapid solidification, a unique microstructure is achieved that rivals the performance of the highest-grade aluminum foundry products. Coupling these material properties with the design freedom provided by AM processes can enable high performance parts with a level of functionality previously impossible to achieve.
Key Properties
- Lightweight
- High strength with good ductility
- Good corrosion resistance
- High thermal conductivity
Markets
Applications:
- Brackets
- Thermal management components
- Waveguides
- Ducts
Powder properties
PART NUMBER | CT PR SCALMALLOY F |
NOMINAL PARTICLE SIZE | 20–63 μm |
APPLICATION | L-PBF1 |
MAXIMUM PARTICLE SIZE | Max 10 wt% > 63 μm2 |
MINIMUM PARTICLE SIZE | Max 10 wt% < 20 μm3 |
LSD PERCENTILE | D10, D50, D903, reported |
ATOMIZATION | Nitrogen gas atomize |
APPARENT DENSITY (G/CM3) | Measured according to ASTM B2124 and reported |
HALL FLOW (S/50G) | Measured according to ASTM B2135 and reported |
1ASTM/ISO 52900: Laser—Powder Bed Fusion (L-PBF), Electron-Beam Powder Bed Fusion (EB-PBF), Directed Energy Deposition (DED)
2ASTM B214 Standard Test Method for Sieve Analysis for Metal Powders
3 ASTM B822 Standard Test Method for Particle Size Distribution of Metal Powders and Related Compounds by Light Scattering
4 ASTM B212 Standard Test Method for Apparent Density of Free-Flowing Metal Powders Using the Hall Flowmeter Funnel
5 ASTM B213 Standard Test Method for Flow Rate of Metal Powders Using the Hall Flowmeter Funnel
Testing of powder will fulfill certification requirements to Nadcap Materials Testing and ISO/IEC 17025 Chemical, per relevant ASTM procedures
Additive manufacturing process guidance
ASTM/ISO 52900: LASER-POWDER BED FUSION (L-PBF)
Laser-Powder Bed Fusion(L-PBF)
Qualified machines: 3D Systems DMP 350. Additive Industries – MetalFab 1. EOS M280/290 and M400. Renishaw RenAM 500Q. SLM Solutions SLM 125, SLM 280, and SLM 500. Concept Laser M2.
Heat treatment
325°C for 4 hours. Inert atmosphere is not necessary.
Hot isostatic pressing (HIP)
HIP may be conducted for microstructure homogenization; removal of residual spatter-induced voids, trapped gas porosity in powder, and keyhole porosities. This can also bring about improved fatigue performance of as-built or heat treated material.
To achieve up to full density (100%): Process components with minimum pressure of 1000 bar, at a temperature of 325°C for 2 hours in inert gas (e.g. argon).
Machinability
Scalmalloy is relatively similar to typical aluminum alloys and can be readily machined in either as-built, heat treated,
or HIPed condition.
TYPICAL MICROSTRUCTURES
CONDITION
TRANSVERSE (X-Y PLANE)
LONGITUDINAL (Y-Z PLANE)
NOTES
Heat treated
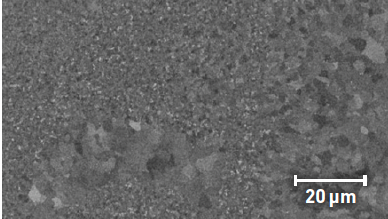
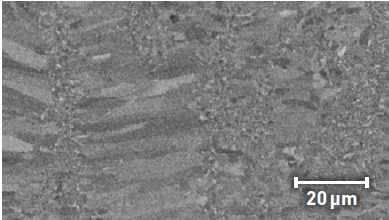
Bimodal microstructure with areas of fine equiaxed grains (< 1 μm) and coarse columnar grains (> 5 μm)
Corrosion resistance
IMPORTANT NOTE: The following 4-level rating scale (Excellent, Good, Moderate, Restricted) is intended for comparative purposes only and is derived from experiences with wrought product. Additive manufactured material may perform differently; corrosion testing is recommended. Factors that affect corrosion resistance include temperature, concentration, pH, impurities, aeration, velocity, crevices, deposits, metallurgical condition, stress, surface finish, and dissimilar metal contact.
Salt Spray (NaCl) | Excellent |
CORROSION TEST RESULTS
SALT WATER SPRAY TEST DIN ISO 50021SS / 5% NaCL, 48H, NO SURFACE PROTECTION | |
CONDITION | AVERAGE CORROSION RATE, MDD |
As-printed surface | No weight loss due to correction, slight weight gain due to salt deposits |
SALT WATER SPRAY TEST DIN ISO 9227-NSS / 50±5 G NaCL/L pH LEVEL: 6.5-7.2 | |||
CONDITION AND METHOD | LAYER THICKNESS (μm) | TEST DURATION (H) | RESULT |
Anodized surface - Lasox | < 2 | 1000 | No corrosion, Rp10 |
Anodized surface - HC | 60–70 | 1000 | No corrosion, Rp10 |
Anodized surface - TE | ~ 30 | 1000 | No corrosion, Rp10 |
Physical properties
PROPERTY |
DENSITY |
THERMAL CONDUCTIVITY |
ELASTIC MODULUS (E) |
At or From |
Room temperature |
Room temperature | 100°C | 200°C |
Room temperature |
English Units |
167 lb/ft3 |
- | - | - |
10.15 Mpsi |
Metric Units |
2670 kg/m3 |
95 W/m·K | 110 W/m·K | 120 W/m·K |
70 GPa |
Typical mechanical properties
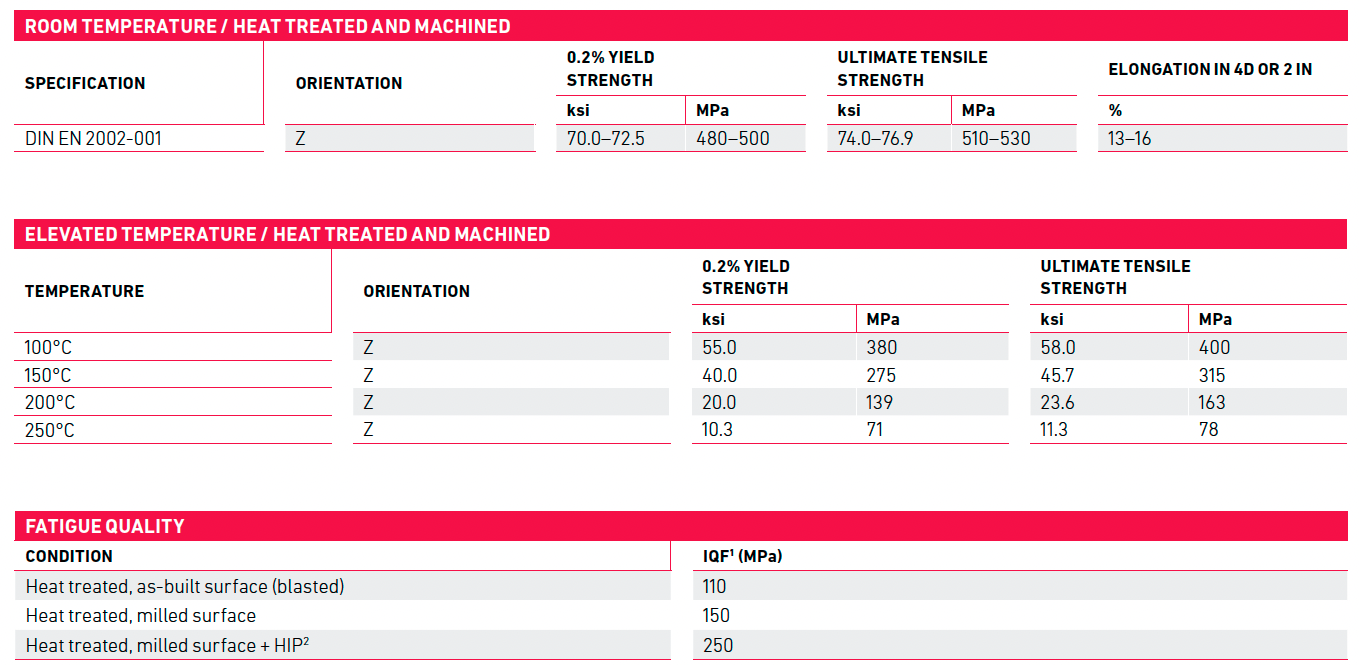
1 The Fatigue Quality Index (IQF) represents the stress level at which the specimen life will reach 100,000 load cycles with a notch factor FT = 1 and an R-Ratio of 0.1
2 Hot Isostatic Pressing (HIP) at 325°C / 1000 bar / 2 hours
For additional information, please
contact your nearest sales office:
The mechanical and physical properties of any additively-manufactured
material are strongly dependent on the processing conditions used to
produce the final part. Significantly differing properties can be obtained by
utilizing different equipment, different process parameters, different build
rates and different geometries. The properties listed are intended as a
guide only and should not be used as design data.
The information and data presented herein are typical or average values
and are not a guarantee of maximum or minimum values. Applications
specifically suggested for material described herein are made solely for the
purpose of illustration to enable the reader to make his/her own evaluation
and are not intended as warranties, either express or implied, of fitness for
these or other purposes. There is no representation that the recipient of
this literature will receive updated editions as they become available.
Unless otherwise specified, registered trademarks are property of
CRS Holdings Inc., a subsidiary of Carpenter Technology Corporation.
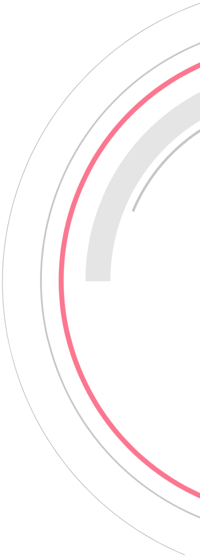